I ran a set of thread tests today, 1/2"-20 threads printed at a layer height of 0.158mm (8 layers per thread) in both PLA (Overture Grey) and PETG (Overture Black)… I tested 1, 1.5, 2, 2.5 and 3 threads in PLA and those plus 3.5 and 4 threads in PETG… I could not test more in the PLA because it would have exceeded the limits of my Force Gauge… Here are the results…
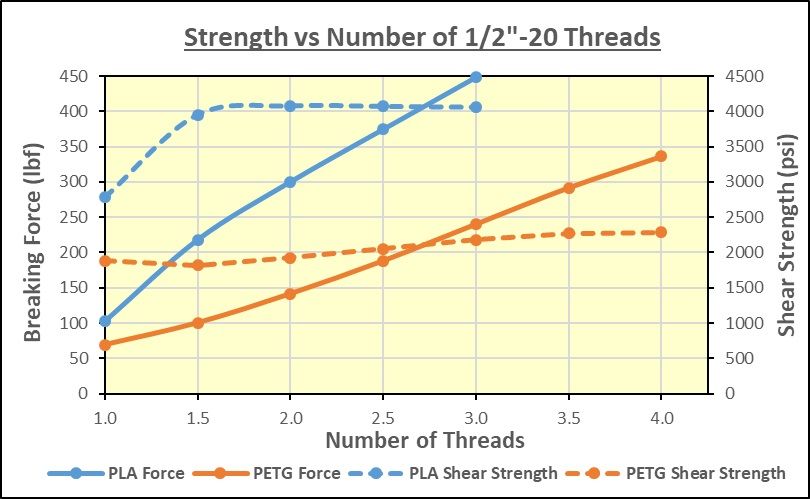
The PLA took about 150 lbf. per thread to break, and the PETG took about 80 lbf. per thread… A single thread is not very reliable for data, as one might expect, but from 1.5 threads up, the data is pretty linear, as you would expect… The dotted lines give the Shear Strength in psi, based on the calculated theoretical area of threads in shear (number of threads x pitch diameter x PI x (pitch/2))… The last number is the theoretical thickness in shear of one thread at the pitch diameter… For 1/2"-20TPI that works out to 0.0368 sq.in. per thread in shear… In theory, those should be straight, horizontal lines (the shear strength should be constant, independant of area)… They are pretty close, so that validates the testing method…
I took photos of the broken test cylinders, and the results were interesting… First the PLA…
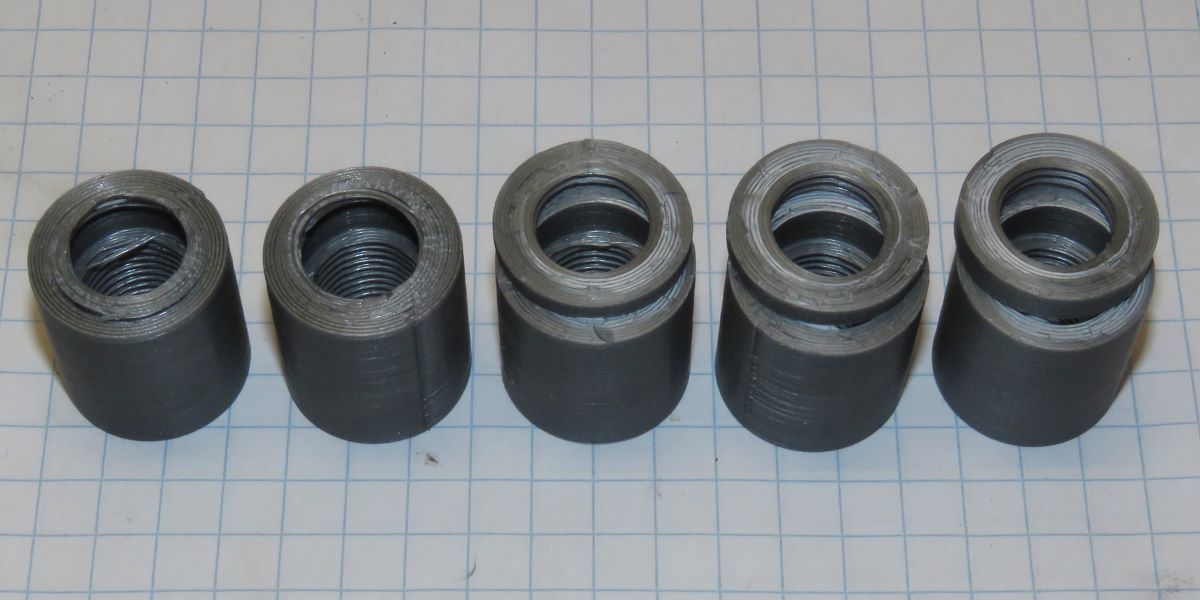
and then the PETG… Both photos had a single thread on the left, increasing in thread count to the right… Click on the pics to enlarge…
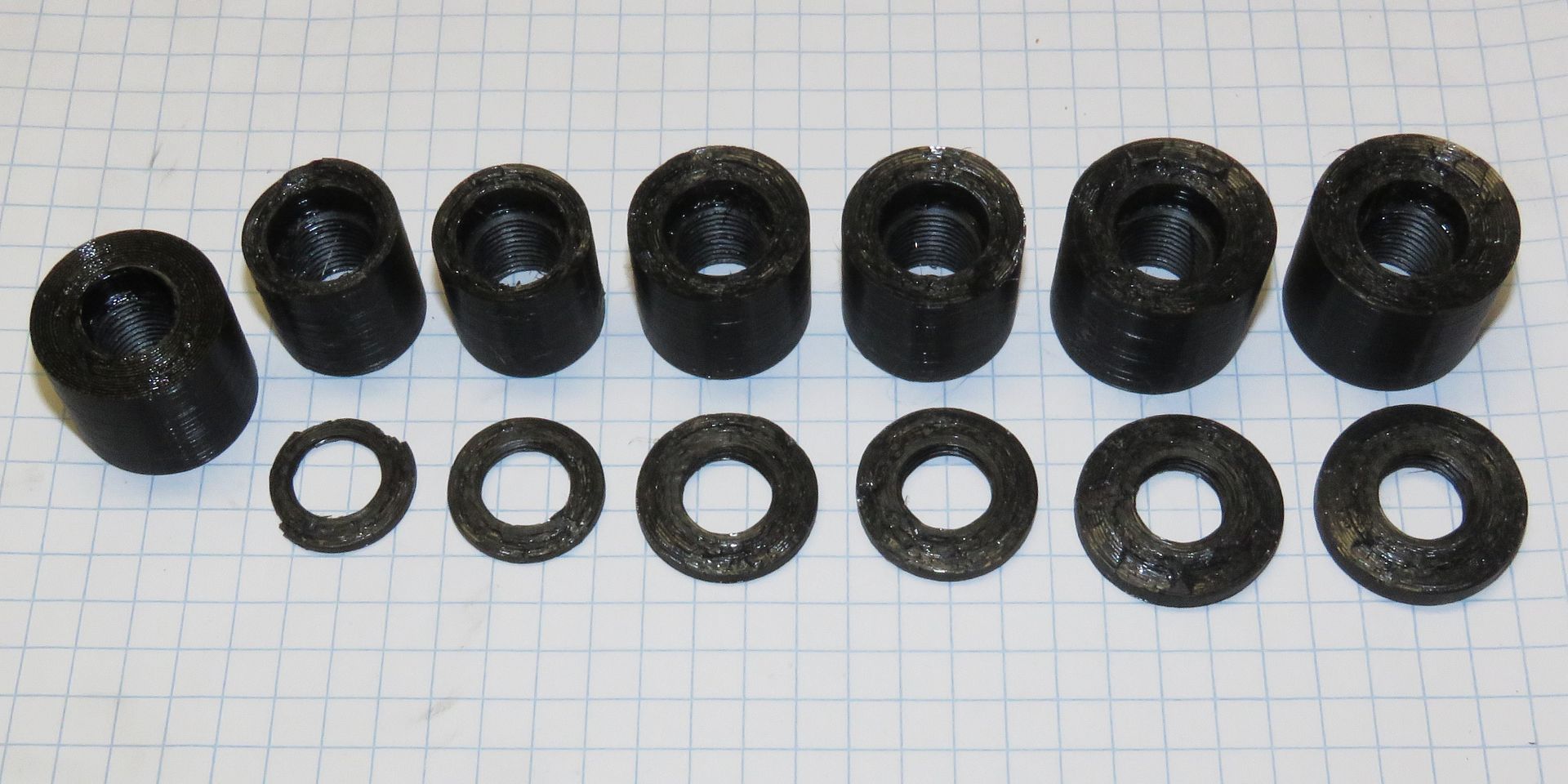
In all cases, other than the very thin thread samples, the failures occurred right where the last thread stopped, where a 14mm diameter internal cylinder provides a precise location where that occurs… The test threads were between that 14mm ID and the outer end of the test samples… Now one might think that showed that the wall of the cylinder at the 14mm diameter was too thin, causing the part to fracture there… In fact, with the PETG I made the OD larger as the thread count increased to help avoid that, to no avail…
I went back and checked my calculations on that portion of the cylinder, and recalculated the theoretical breaking force, using my measured tensile strength in the “Z” direction for these two materials… The area of that cylindrical portion is (20^2 - 14^2) x PI/4 = 160 mm^2 = 0.248 sq.in… The Overture PLA had a tensile strength of 4750 psi when printed at 220C (which is what I used for the thread test), which should take (4750 x 0.248) = 1178 lbf. to break, requiring nearly 4 times as much as the 300 lbf. it took to break the middle sample, which had 2 threads… The Overture PETG had a measured tensile strength of 3650 psi at 240C (the thread printing temperature), which would take (3650 x 0.248) =905 lbf. to break, over 9 times the 100 lbf. it took to break the 1.5 thread long sample… Additionally, if it was the wall thickness of the 14mm ID section that was the weak point, it would have failed at the same force in every test, which it did not… Also, the thicker cylinders I used for the longer threads in the PETG samples, would have showed an increase in force required to break them… The largest OD samples I used were 26mm, having a cross sectional area at the 14mm ID more than double that of the 20mm cylinders…
So, how are the samples breaking?.. If you look closely at the thicker thread samples in PETG (right end) you will notice that the samples broke along a cone shape, and did not simply rip between the layers… None of the samples (except the very thinnest ones, which stripped out) broke anywhere but at the inner end of the threads, which of course is where the stress is the highest… Although every thread imposes load on the cylindrical wall outside of it, those loads add up and peak where the threads end at the 14mm ID recess… Therefore, that is the point that tears first, and once that rip starts, it just zippers across the outer tube, following the line of maximum stress, which is supported less and less as each layer of the print breaks…
The fact that the data behaved exactly as it should, and that the Shear Strength was less than the Tensile Strength of the material (in the Z direction), I think these are valid and reliable tests… How thick an outer structure would you need before you would see even 4 threads pull straight out the end?.. I dunno, but way more than the 6mm wall in those 26mm OD samples…
Bob